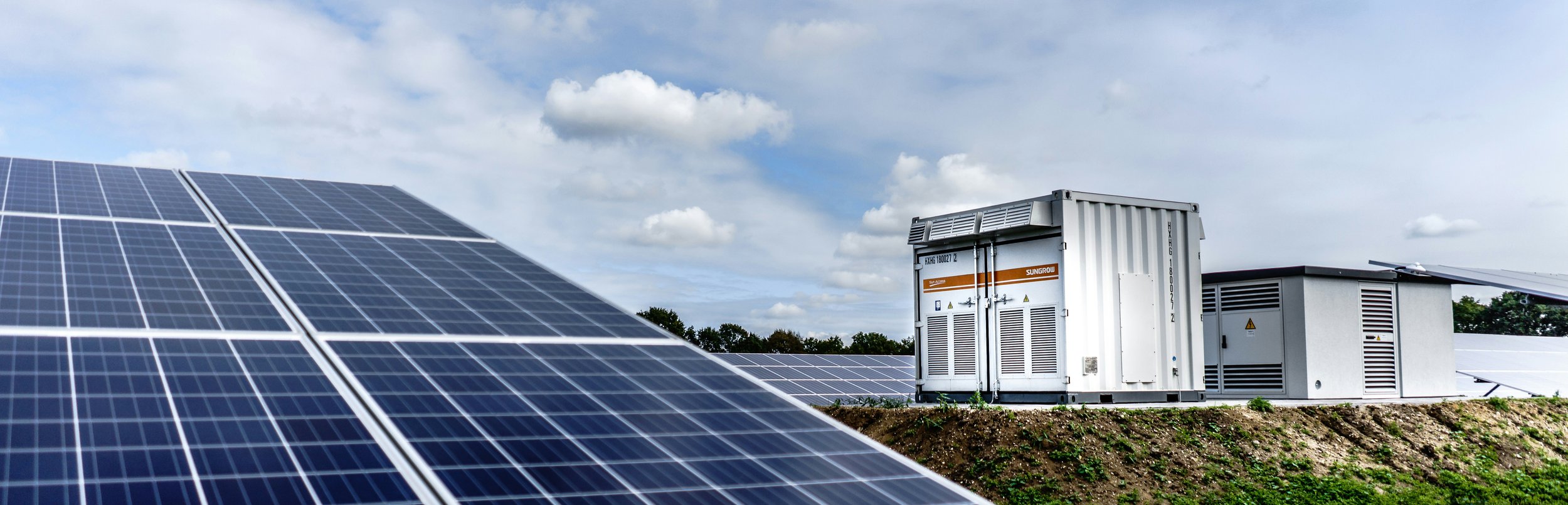
Case Study -
Solar Inverters
Locations near the equator are often ideal sites for solar power facilities due to the direct, reliable, and extended exposure to the sun. However, these areas experience intense heat which can cause equipment to function inefficiently and experience frequent mechanical breakdowns. Prolonged exposure to such intense temperatures reduces equipment longevity as well. With this information in mind, Heat Inverse carried out a pilot with a major power distributor at two solar farms in Arizona.
Solar inverter covered with film.
CoolFilm was installed on solar power inverters and then compared over time to similar on-site units: an unmodified “control” inverter, and another covered by a large shade structure. The inverter covered by CoolFilm had the lowest average cabinet temperatures and highest average heat sink temperature for each month the of test, indicating that the CoolFilm inverter was staying the coolest while converting the most electricity. Additionally, the CoolFilm inverter had fewer derating events on hot days.
The CoolFilm inverter favorably compared to control inverters as well as similar units installed under shade structures (pictured here).
The benefits of this cooling are captured in many ways including:
● Increased output driving higher total production.
● Fewer derating events driving increased daily revenues.
● Decreased maintenance calls meaning lower expenses.
● Fewer outages leading to reliable revenues.
● Increased longevity allowing for longer-term profits.
“The temperature will reduce maintenance needs by 50%.”
“The film works better than a shade structure and costs 7 times less.”
-Feedback from the utility